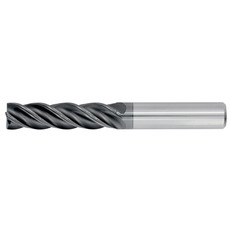
Skookum High Performance and Ultra High Performance Carbide End Mills: Revolutionizing Metal Cutting
In the world of CNC machining, choosing the right tool for the job has always been crucial for efficiency, precision, and cost-effectiveness. Traditionally, roughing end mills have been the go-to choice for removing material quickly, with finishing tools stepping in for the final touches. However, the introduction of Skookum High Performance (HP) and Ultra High Performance (UHP) carbide end mills has shifted the paradigm, making roughing end mills a thing of the past.
The Evolution of Carbide End Mills
Carbide end mills have long been a staple in the machining industry, valued for their durability and efficiency. Yet, standard carbide tools often required the use of a separate roughing end mill to handle the initial bulk material removal, especially in tough alloys or high-hardness materials.
Skookum has taken carbide technology to the next level with their High Performance and Ultra High Performance carbide end mills. These advanced tools are designed not just to finish with precision, but also to handle the demanding work of roughing with ease. Their advanced coatings, geometries, and substrate materials mean they can achieve feed rates and speeds traditionally reserved for dedicated roughing tools. Let’s explore why Skookum HP and UHP carbide end mills are replacing roughing mills in modern machining.
Key Features of Skookum HP and UHP Carbide End Mills
-
Advanced Tool Geometry: The cutting-edge designs of Skookum HP and UHP mills are optimized for efficient chip evacuation, aggressive cutting, and stability under load. These geometries allow for high material removal rates (MRR) while reducing the forces acting on the tool, minimizing vibrations, and preventing tool deflection—common issues with traditional roughing mills.
-
Superior Coatings: Skookum's high-performance mills are coated with specialized materials that enhance heat resistance, reduce friction, and prolong tool life. This means they can maintain peak cutting performance at higher temperatures, enabling faster feeds and speeds.
-
High Toughness and Wear Resistance: The premium carbide substrate used in Skookum’s end mills offers superior toughness and resistance to wear. This durability means they can handle interrupted cuts, heavy loads, and high speeds without the need for frequent replacements.
-
Versatility: These end mills are designed to be "one-tool solutions." Skookum HP and UHP mills can effectively rough and finish, eliminating the need for multiple setups and tool changes. This versatility leads to less downtime, reduced tool inventory, and simplified workflows.
Why Roughing Mills Are No Longer Necessary
The primary purpose of roughing mills has always been to hog out material quickly and efficiently, but Skookum's High Performance and Ultra High Performance end mills achieve comparable or superior results with a single tool. Here’s how:
1. Comparable Feeds and Speeds
Skookum HP and UHP mills are capable of handling aggressive feeds and speeds that match or exceed those of traditional roughing mills. The combination of optimized geometry and advanced coatings means that these mills can maintain cutting stability, even at high rates of material removal. This allows machinists to rough and semi-finish in one pass, saving time and improving efficiency.
2. Reduced Tool Changeovers
By eliminating the need for separate roughing and finishing tools, Skookum’s carbide end mills cut down on tool changeovers, which reduces cycle times and increases productivity. For manufacturers, this translates into higher throughput, lower costs, and increased profitability.
3. Improved Surface Finish from the Start
Roughing mills are notorious for leaving behind heavy tool marks that require extensive finishing passes. In contrast, Skookum HP and UHP end mills produce a finer surface finish even during the roughing stage, often requiring fewer finishing passes or lighter touch-up work afterward. This makes them ideal for applications that demand both precision and speed.
4. Cost Efficiency Over Time
While high-performance end mills may have a higher initial cost compared to traditional roughing mills, their longer lifespan, versatility, and reduced need for tool replacements make them a more cost-effective choice in the long run. The extended tool life means fewer purchases, less downtime, and a streamlined workflow.
Case Study: Real-World Application
Manufacturers across various industries—from aerospace to automotive—have seen significant improvements by switching to Skookum High Performance and Ultra High Performance end mills. For example, a CNC machine shop that previously relied on dedicated roughing mills saw a 30% reduction in machining time after adopting Skookum’s high-performance tools. By using fewer tools and maintaining high feed rates throughout the process, they achieved faster turnaround times and enhanced product quality.
Making the Switch to Skookum HP and UHP End Mills
If you're still relying on a mix of roughing and finishing tools, it might be time to reconsider your approach. Skookum High Performance and Ultra High Performance carbide end mills are designed to handle the full spectrum of machining tasks with unmatched efficiency. Here’s what to keep in mind when making the switch:
-
Check Cutting Parameters: Skookum provides detailed guidelines on optimal feeds and speeds for their HP and UHP mills. These parameters are key to achieving the best performance and should be adhered to for maximum efficiency.
-
Use High-Quality Coolants: While Skookum end mills are designed to handle high temperatures, proper coolant selection will further extend tool life and enhance surface finish.
-
Optimize Tool Paths: Maximize the performance of Skookum mills by using CAM software to optimize tool paths, ensuring consistent chip load and even tool wear.
Conclusion
Skookum's High Performance and Ultra High Performance carbide end mills are game-changers in the world of machining. By delivering the same, if not better, feeds and speeds as traditional roughing mills—while providing superior versatility and precision—these tools are setting new standards for efficiency and quality. Investing in Skookum’s technology not only eliminates the need for dedicated roughing mills but also enhances overall productivity, making it a smart choice for modern CNC operations.
For those looking to streamline processes and improve machining capabilities, the time is now to make the shift to Skookum HP and UHP carbide end mills. The future of CNC machining is here, and it's faster, smarter, and more efficient than ever before.
Robert McDonald is the President and founder of Skookum Tools Ltd. est September 2000.
His experience in dealing with a large variety of manufacturing industry clients has helped him
become a valuable resourse to industry specialists.