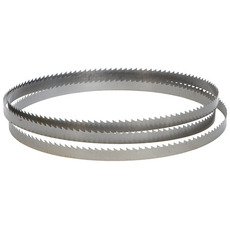
How to identify and solve the most common problems with bandsaw blades.
Having troubles with your bandsaw blades can be frustrating and costly. By identifying specificaly what the issue you are having is, and working through these suggestions, you will be able to quickly resolve most, if not all issues. If after going through this guide you are still having troubles, please feel free to give us a call at 1-888-665-6936 or click on the “Chat with us here” for further assistance.
The following information comes from one of the best bandsaw blade manufacturers in the USA – M.K. Morse
Problem | Problem Cause | Solutions |
---|---|---|
|
|
|
|
|
|
|
|
|
|
|
|
|
|
|
|
|
|
|
|
|
|
|
|
|
|
|
|
|
|
|
|
|
|
|
|
|
|
If you are still having issues after going through this guide, please feel free to reach out to us for further support!
1-888-665-6936